CNC Machining: A Revolution in Precision Manufacturing
CNC machining has revolutionized manufacturing, offering a precise and efficient process for making components and pieces across a wide array of industries. This advanced technology uses computer-controlled machines to carry out cutting drill, milling and various other processes on materials such as metals, plastics and wood. The precision that can be achieved with CNC machining is unparalleled that allows intricate designs to be carried out with incredible precision. By replacing manual intervention with automation, CNC machines have significantly diminished the risk that human error will occur and has also improved production speed. This combination of precision and effectiveness has led to CNC machines an essential aspect of modern manufacturing.
The core feature of CNC machining is the ability to transform digital drawings into physical parts. Utilizing computer-aided design (CAD) software, engineers and designers create elaborate 3D models for the desired part. These digital designs are then transferred into precise instructions called “G-code,” which the CNC machine uses to execute tasks like cutting, drilling and milling. This control is digital, which allows for the highest level of precision that manual milling cannot achieve. Additionally, once a design is entered into the machine, it is repeatable without any issues, and produce similar parts in large numbers without needing manual adjustments. This repeatability is essential in industries where precision and homogeneity are vital.
Efficiency is another major benefit for CNC processing. Once the design is programed in the machine it is able to run in a controlled manner with multiple functions without constant personal intervention. Automatization results in quicker production and better consistency in the quality of the products produced. Furthermore, CNC machines can operate constantly, which means manufacturers can make parts round the clock, which can increase overall output. Contrary to conventional methods of machining, which require experienced machinists to control the tools, CNC machining offers a considerable reduction in costs for labor and also the chance of errors made by human beings, making it an economical solution for massive production.
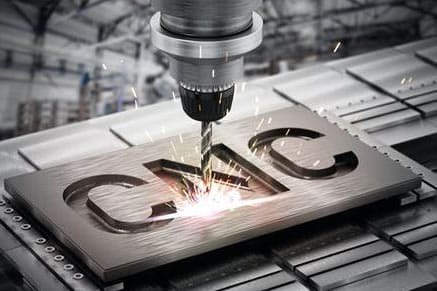
One of the major components of CNC machining is the utilization of computer-aided designing along with computer-aided software for manufacturing. CAD software lets engineers design precise 3D models of the parts to be produced, while CAM software transforms these drawings into machine instruction. The seamless integration of manufacturing and design ensures the finished product is in line with the original design specs. Moreover, CAD/CAM software enables rapid prototyping. It allows companies to quickly test and refine their concepts before going into massive production. It is possible to modify designs and create prototypes provides businesses an advantage in sectors where speed and innovation to market are essential. To acquire more details please check out Premiumparts
Despite its many advantages, CNC machined parts are not without its problems. One of the primary barriers that many businesses face, particularly small and medium-sized enterprises are the initial capital investment necessary. CNC machines cost more than conventional machining equipment, as well as an expense for specialized software, maintenance, and operator training to consider. However, the long-term benefits–such like lower costs for labor as well as faster cycles of production and increased quality of parts – often justify the initial cost. In addition, the rise in CNC machining service providers allows those who do not have capital to put into their machines to benefit from the technology. The service providers are able to create specific parts at the request of customers which is a cost-effective choice to businesses who require precision manufacturing without the initial costs.
Another obstacle in CNC machining lies in the programing and setting of CNC machines. While CNC machines reduce a significant amount all manual labor in manufacturing processes however, they require experienced technicians to create and input the required programs. These technicians must have expertise in CAD/CAM (Computer-Aided Design/Computer-Aided Manufacturing) software and understand the specific machining requirements of each project. Unintentional programming mistakes can create defective parts or materials being wasted, as well as machines being shut down. Also, the initial setting up of the CNC machine may take time, particularly with large-scale projects that require several tools or processes. When the machine has been properly installed and programed it will be able to produce components that are extremely fast and precise, minimizing the potential for errors in subsequent runs.